Page 1 of 1
A-pillar surgery
Posted: Fri Sep 06, 2019 3:34 am
by Adam in Wa
Re: A-pillar surgery
Posted: Fri Sep 06, 2019 4:44 am
by June J
Nice going! Its a tricky area to work in.
Cheers
Ian
Re: A-pillar surgery
Posted: Mon Sep 09, 2019 12:06 am
by Adam in Wa
Re: A-pillar surgery
Posted: Mon Sep 09, 2019 3:34 am
by June J
Made somewhere easier with tig/mig and cutting discs

Re: A-pillar surgery
Posted: Mon Sep 09, 2019 9:00 am
by Gordon_M
My TD20 was particularly affected in that area and it all came down to mice - and their residue. It is worth noting that anything that needs you to cut through here should be thoroughly cleaned, flushed, and disinfected first, then use gloves and a dust mask.
The upside is that the metal in these pillars is relatively thick, so it is possible to cut out, remove, and plate back in large sections without losing the shape. A spot weld cutter lets you remove and then refit the drip rail too if you have to.
Re: A-pillar surgery
Posted: Mon Sep 09, 2019 9:45 pm
by Adam in Wa
Gordon is correct about the mice and spot weld cutter. I have a 1971 Dodge Challenger. When I bought it mice had been nesting in the wiper cowl area for years. Their urine had completely rotted out the firewall. I figured I could drill out the spot welds on the wiper cowl, sandblast the area, and weld in patches. But naturally it didn’t work out that way. The cowl had maybe thirty spot welds and I tried to be cheap and use Chinese spot weld cutters. They were advertised as M2 tool steel and were relatively inexpensive, but looked great. Each bit lasted for about six spot welds. When it became obvious I would have to remove the firewall itself I was looking at many more spot welds. I stepped up and got some American made bits, and what a difference it made. I only used one bit for the firewall, the roof, floor, deck filler, and trunk pans; must have been hundreds of spot welds easily.
If you want to see pics, here is a link to my photo album:
https://ImageEvent.com/adamell/wiperparts
Btw, I get a kick out of pics 235 & 236.
Re: A-pillar surgery
Posted: Sat Sep 14, 2019 11:59 pm
by Adam in Wa
It still needs a little work, and seam sealer before paint.
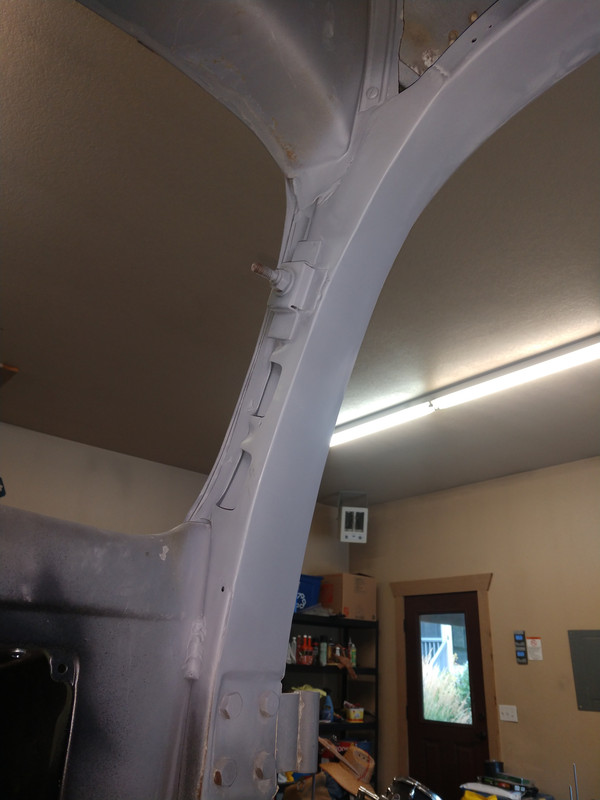
Re: A-pillar surgery
Posted: Thu Sep 19, 2019 5:14 am
by Kaegi
nice job!
